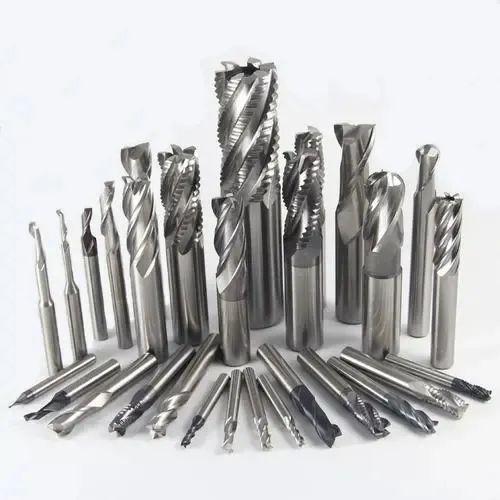
Современите материјали за алати за сечење имаат повеќе од 100 години историја на развој, од јаглероден челик за алати до челик за алати со голема брзина,цементиран карбид, керамичка алаткаисупертврди материјали за алатиВо втората половина на 18 век, оригиналниот материјал за алати бил главно јаглероден челик за алати. Бидејќи во тоа време се користел како најтврд материјал што можел да се преработи во алати за сечење. Сепак, поради неговата многу ниска температура отпорна на топлина (под 200°C), јаглеродните челици за алати имаат недостаток што веднаш и целосно се заматуваат поради топлината на сечење при сечење со голема брзина, а опсегот на сечење е ограничен. Затоа, со нетрпение очекуваме материјали за алати што можат да се сечат со голема брзина. Материјалот што се појавува за да го одрази ова очекување е брзорезен челик.
Брзорезниот челик, познат и како преден челик, бил развиен од американски научници во 1898 година. Не е толку важно што содржи помалку јаглерод од јаглеродниот челик за алати, туку што е додаден волфрам. Поради улогата на тврдиот волфрам карбид, неговата тврдост не се намалува под услови на висока температура, а бидејќи може да се сече со брзина многу поголема од брзината на сечење на јаглеродниот челик за алати, се нарекува брзорезен челик. Од 1900 до 1920 година се појавил брзорезен челик со ванадиум и кобалт, а неговата отпорност на топлина била зголемена на 500~600 °C. Брзината на сечење на челикот за сечење достигнува 30~40 m/min, што е зголемено за речиси 6 пати. Оттогаш, со серијализацијата на неговите составни елементи, се формирани брзорезни челици од волфрам и молибден. Тој сè уште е широко користен до денес. Појавата на брзорезниот челик предизвика...
револуција во обработката на сечење, значително подобрувајќи ја продуктивноста на сечењето метал и барајќи целосна промена во структурата на машинската алатка за да се прилагоди на барањата за перформанси на сечење на овој нов материјал за алати. Појавата и понатамошниот развој на нови машински алати, пак, доведоа до развој на подобри материјали за алати, а алатите беа стимулирани и развиени. Во новите услови на производствена технологија, алатите од брзорезен челик исто така имаат проблем со ограничување на издржливоста на алатот поради топлината на сечење при сечење со голема брзина. Кога брзината на сечење достигнува 700 °C, брзорезниот челик
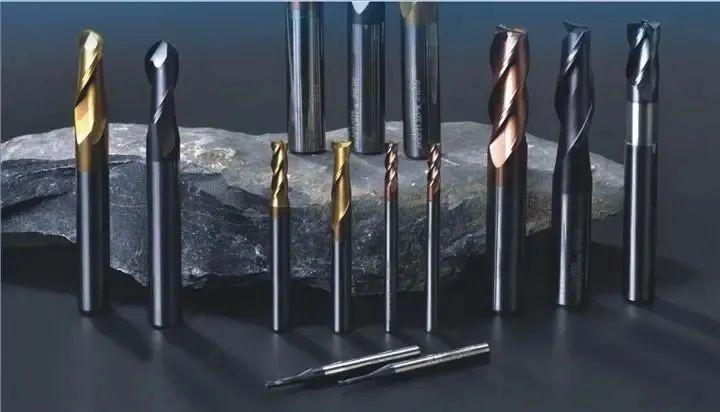
Врвот е целосно тап, а при брзина на сечење над оваа вредност, целосно е невозможно да се сече. Како резултат на тоа, се појавиле карбидни материјали за алати кои одржуваат доволна тврдост под услови на повисока температура на сечење од горенаведените и можат да се сечат на повисоки температури на сечење.
Меките материјали можат да се сечат со тврди материјали, а за да се сечат тврди материјали, потребно е да се користат материјали што се поцврсти од неа. Најтврдата супстанца на Земјата во моментов е дијамантот. Иако природните дијаманти одамна се откриени во природата и имаат долга историја на нивно користење како алатки за сечење, синтетичките дијаманти се успешно синтетизирани уште во раните 50-ти години на 20 век, но вистинската употреба на дијамантите за широко производствоматеријали за индустриски алатки за сечењесè уште е прашање на последните децении.
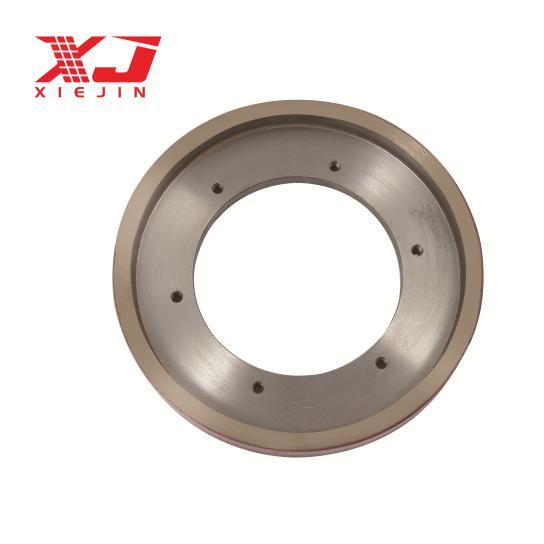
Од една страна, со развојот на модерната вселенска технологија и воздухопловната технологија, употребата на современи инженерски материјали станува сè позастапена, иако подобрениот брзорезен челик, цементираниот карбид инови керамички материјали за алатиПри сечењето на традиционалните обработливи парчиња, брзината на сечење и продуктивноста на сечење се дуплираат или дури и се зголемуваат десетици пати, но кога се користат за обработка на горенаведените материјали, издржливоста на алатот и ефикасноста на сечење се сè уште многу ниски, а квалитетот на сечење е тешко да се гарантира, понекогаш дури и не е можно да се обработи, поради што е потребно да се користат поостри и поотпорни на абење материјали за алати.
Од друга страна, со брзиот развој на современотопроизводство на машинии преработувачката индустрија, широката примена на автоматски машински алати, центри за обработка со компјутерска нумеричка контрола (CNC) и беспилотни работилници за обработка, со цел дополнително да се подобри точноста на обработката, да се намали времето за промена на алатот и да се подобри ефикасноста на обработката, се поставуваат сè поитни барања за потрајни и постабилни материјали за алати. Во овој случај, дијамантските алати брзо се развија, а во исто време, развојот наматеријали за дијамантски алаткиисто така беше многу промовиран.
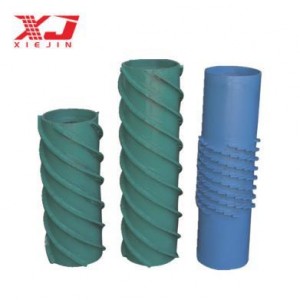
Материјали за дијамантски алаткиимаат низа одлични својства, со висока точност на обработка, брза брзина на сечење и долг век на траење. На пример, употребата на алатки од Compax (поликристални дијамантски композитни листови) може да обезбеди обработка на десетици илјади делови од клипни прстени од силициумска алуминиумска легура, а нивните врвови на алатките се во основа непроменети; Обработката на алуминиумски лопатки за авиони со глодалки со голем дијаметар од Compax може да достигне брзина на сечење до 3660 m/min; Овие се неспоредливи со карбидните алатки.
Не само тоа, употребата наматеријали за дијамантски алаткиисто така може да го прошири полето на обработка и да ја промени традиционалната технологија на обработка. Во минатото, обработката со огледала можеше да се користи само со процес на мелење и полирање, но сега не само природни монокристални дијамантски алатки, туку во некои случаи може да се користат и PDC супер тврди композитни алатки за супер прецизно сечење, за да се постигне стругање наместо мелење. Со примена насупер тврди алатки, се појавија некои нови концепти во областа на машинската обработка, како што е употребата на PDC алатки, ограничувачката брзина на стружење повеќе не е на алатката, туку на машинската алатка, а кога брзината на стружење надминува одредена брзина, обработуваниот дел и алатката не се загреваат. Импликациите од овие револуционерни концепти се длабоки и нудат неограничени перспективи за модерната машинска индустрија.
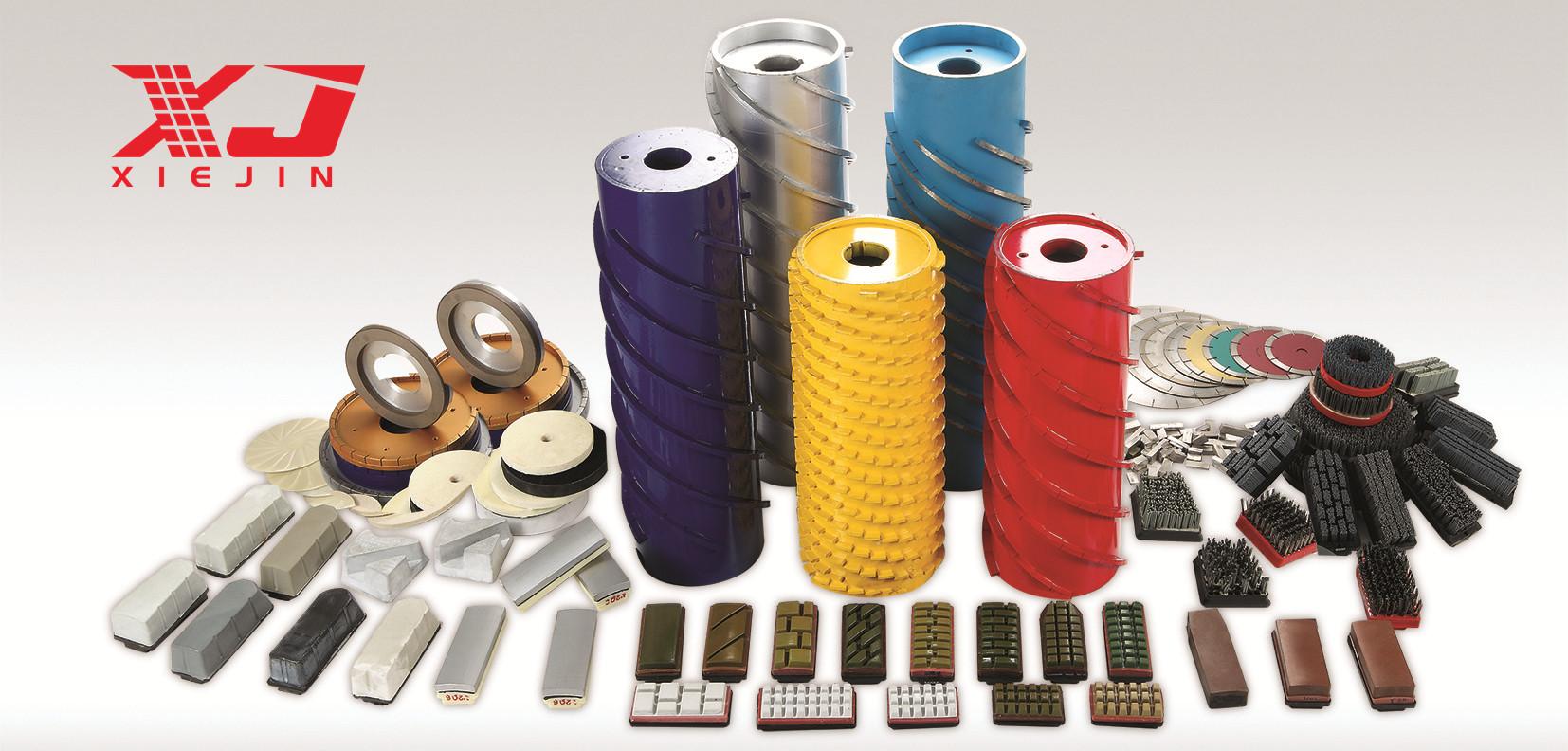
Време на објавување: 02.11.2022